A bit of knowledge about dyeing
Pattern dyeing probably started with someone wanting to add a beautiful pattern (dye) a piece of cloth. The oldest example of that is believed to be tie dyeing. And, among the diverse range of techniques for dyeing patterns, I would like to talk about tie dyeing, print dyeing and yuzen dyeing.
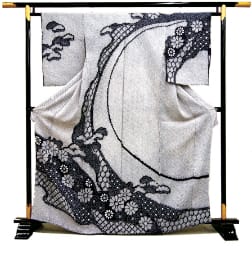
Tie dyeing
Folding, binding, stitching, covering and other such techniques all create patterns by preventing dye from penetrating parts of the cloth being dyed, with the oldest examples said to be housed in Shosoin (an ancient repository of Todaiji Temple, Nara) dating back to the Nara period (710-794). Tie dyeing is found across the globe, in India, Southeast Asia and other places, making it a ubiquitous form of pattern dyeing, ingrained into the psyche of common folk, doubtless leading to the highly technical dyeing technique of “tsujigahana” (vivid images of flowers on a white backgrounds) developed across the Muromachi (1338-1573) and Momoyama (1573-1615) periods – a technique made popular by people of high rank, such as samurai society.
Tie dyeing comes in many gorgeous forms, including cotton indigo dyeing as well as hitta-shibori and kanoko-shibori on silk fabrics. Kanoko-shibori, flourishing in the middle of the Edo period (1603-1868), are extravagant works requiring master artisans to spend, in some cases, many years binding small gatherings of silk (a few millimeters each) to create a dot pattern.
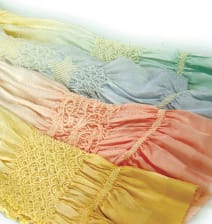
Stencil dyeing
The pattern is cut out from a stencil board, which is made from layers of Japanese “washi” paper stiffened by persimmon juice, starch (nori) is then applied to the cloth exposed by the stencil and the cloth dyed (resist printed) to produce the pattern. There also is a method for directly coloring the stenciled areas, as well.
The ceremonial garments of samurai warriors were dyed using resist printing, with patterns so intricate as to look at times like a solid color, and each one different for each feudal domain. For the really intricate patterns that involved 800 to 1200 tiny resist dots per three-centimeter square, the only way to produce the pattern was to use Ise (present day Mie) stencil paper; thus, Kyoto artisans ordered the Ise stencil paper to create their miniscule patterns, which developed into what is known as Edo-komon (Edo-dyed cloth) and Kyo-komon (Kyoto-dyed cloth).
Yuzen dyeing
Miyazaki Yuzensai, a fan painter, is believed to have been the first “yuzen” artist in the early days of the Edo period. He used a fan painting to create a pattern for wadded silk gowns (kosode) that he produced by dyeing. The pictorial expressiveness of such patterns became very popular. And, by using fine forms of starch for the paste on the contour lines dividing colors, those colors could be made to bleed into each other in varying degrees. For this work, itome-nori, or paste for fine-line printing, is squeezed from a piping cornet with metal nozzle to line sketch the motif onto the fabric. By the Meiji period (1868-1912), Hirose Jisuke had invented katagami yuzen, or paper-pattern yuzen, which made mass production of yuzen-dyed fabrics possible. And, by the Showa period (1926-1989), a simple fine-line latex was being broadly used. There were many skills used in hand-drawn yuzen, including design, motif pattern, under picture, fine-line paste application, ji-ire (background filling), coloring, fuse-nori (blocking paste), background dyeing, steaming, water washing and other such processes, all of which required the skills of veteran artisans who specialize in each process, with a coordinator overseeing them, to ensure that individual works of beauty could be created by a team of artisans scattered across several neighborhoods.
Photo: Dyed fabric (Kyoto Shibori Museum)